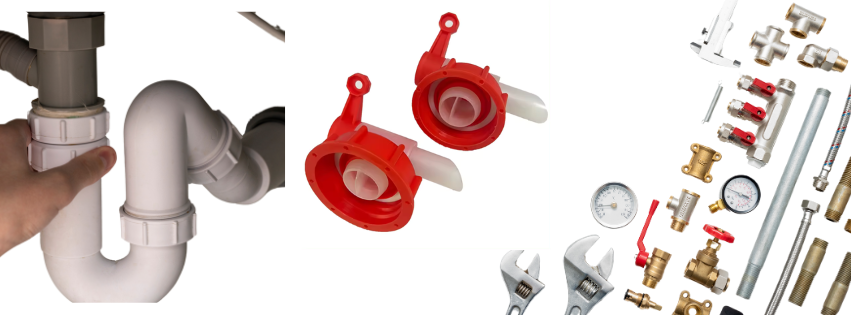
The Evolution of Drum Taps and Plastic Fittings in Modern Industry
In the vast and varied world of industrial manufacturing, two seemingly unrelated components, Drum Taps and Plastic Fittings, have become essential elements across multiple sectors. From chemical processing plants to the beverage industry, these components have revolutionized efficiency, safety, and environmental responsibility.
The Rise of Drum Taps in Industrial Applications
Drum Taps have been a cornerstone of fluid management in industries for decades. Historically, they were primarily made from metal, specifically brass or stainless steel, due to the material's strength and resistance to corrosion. These early Drum Taps were designed to control the flow of liquids from large containers like barrels and drums, which are commonly used to store and transport various liquids, including chemicals, oils, and even food products.
The design of Drum Taps is straightforward yet highly effective. A typical tap features a spout and a lever or handle that, when turned, opens or closes the flow of liquid. Over time, the design has evolved to incorporate features like self-closing mechanisms, which enhance safety by reducing the risk of spills and leaks. These developments are crucial in industries where hazardous liquids are handled, as even a small spill can have significant environmental and safety consequences.
The Introduction of Plastic Fittings and Their Impact
Plastic Fittings, on the other hand, represent a more recent innovation in the industrial world. Initially, metal fittings were the standard, but with the advancement of polymer science, plastic fittings have emerged as a viable and often superior alternative. They are now ubiquitous in systems that require the connection of pipes, hoses, or other conduits to transport fluids or gases.
The advantages of Plastic Fittings are numerous. First and foremost, they are resistant to corrosion, a common problem with metal fittings. This resistance makes them ideal for use in environments where they are exposed to chemicals or moisture. Furthermore, Plastic Fittings are lightweight, making them easier to handle and install, which can significantly reduce labor costs. Their flexibility also allows for more versatile applications, as they can be molded into various shapes and sizes to fit specific requirements.
The Intersection of Drum Taps and Plastic Fittings
The integration of Drum Taps and Plastic Fittings has opened new avenues for innovation and efficiency. In industries where drums are used to store and transport liquids, the combination of these two components ensures a secure and efficient system for fluid management. For instance, Plastic Fittings can be used to connect a Drum Tap to a larger piping system, facilitating the transfer of liquids from the drum to other parts of a facility.
One of the significant benefits of using Plastic Fittings in conjunction with Drum Taps is the reduction of contamination risks. Since Plastic Fittings are non-reactive with many chemicals, they prevent unwanted chemical reactions that could compromise the purity of the liquid being stored or transferred. This feature is particularly important in industries like pharmaceuticals or food and beverage, where maintaining product integrity is paramount.
Moreover, the ease of installation and replacement of Plastic Fittings means that maintenance of Drum Taps has become less cumbersome. In the past, replacing a faulty tap or fitting often required extensive downtime, leading to production delays. However, with the advent of modular Plastic Fittings, parts can be swapped out quickly and efficiently, minimizing disruptions to operations.
Environmental Considerations
In today’s industrial landscape, sustainability and environmental responsibility are key considerations. Drum Taps and Plastic Fittings play a significant role in supporting these goals. Modern Drum Taps are designed to minimize leaks and spills, reducing waste and the potential for environmental contamination. Additionally, many Plastic Fittings are now made from recyclable or biodegradable materials, further lessening their environmental impact.
The lightweight nature of Plastic Fittings also contributes to a reduction in transportation emissions. Since they are lighter than their metal counterparts, less energy is required to transport them, whether in bulk shipments to industrial facilities or in the movement of finished products that incorporate these fittings.
Innovations on the Horizon
As technology continues to advance, the future of Drum Taps and Plastic Fittings looks promising. Researchers are exploring new materials and designs that will further enhance the durability, safety, and environmental friendliness of these components. For example, there is ongoing research into bio-based plastics, which could be used to manufacture Plastic Fittings that are not only recyclable but also derived from renewable resources.
In the realm of Drum Taps, smart technology is beginning to make its mark. Some companies are developing taps equipped with sensors that can monitor liquid levels, flow rates, and even detect leaks in real time. This information can be transmitted to a central control system, allowing for better oversight and management of liquid storage and transfer processes. The integration of smart Drum Taps with automated Plastic Fittings could lead to highly sophisticated fluid management systems that are both efficient and environmentally sustainable.
Conclusion
Drum Taps and Plastic Fittings, though simple in their design and function, are critical components in the machinery of modern industry. Their evolution from basic, manually operated devices to sophisticated, eco-friendly solutions reflects the broader trends in industrial technology towards greater efficiency, safety, and sustainability.
As industries continue to grow and evolve, the demand for reliable and innovative fluid management solutions will only increase. Drum Taps and Plastic Fittings will undoubtedly remain at the forefront of this evolution, helping to shape a future where industrial processes are not only more efficient but also more responsible stewards of the environment. Whether in a chemical plant, a food processing facility, or a pharmaceutical laboratory, these unassuming components will continue to play a pivotal role in ensuring that the wheels of industry keep turning smoothly